Author: Mathias Lia Carlsen
* This is a short-version of SPE-199982-MS that will be presented on the SPE Canada Unconventional Resources Conference 18 March 2020 in Calgary, Canada. The manuscript can be found attached to this blog post.
CGR Normalization – What is it?
Black oil tables are generated assuming a fixed surface process, but in reality, separator conditions change through time. Hence, there is a risk for inconsistencies between the rates used in history matching (assumes constant separator conditions) and the actual measured rates (changing separator conditions in the field). If surface process separator conditions are changing significantly over time, a “correction” to a set of constant separator conditions might be needed for
- Consistent well-to-well performance comparison
- Consistent usage of black oil tables in history matching (using RTA/PTA or res. simulation)
- Consistent analysis of condensate-gas ratio (CGR) performance over time
The correction is referred to as CGR normalization, as we “normalize” for changing separator conditions (remove the effect of changing separator conditions). The objective of this paper is to provide a qualitative framework of when CGR normalization is important and how to do this when it is found to be important.
CGR Normalization – When is It Important?
To understand how changing separator conditions can impact the producing CGR over time, a wide range of wellstream compositions were analyzed and processed through a set of different separator conditions (psep, Tsep). The separator temperature range analyzed was 50 to 150 F, while the separator pressure range was 50 to 1000 psia; typical separator operating conditions. To quantify how sensitive the total CGR[1] is to different separator conditions, the relative difference, delta, between the maximum (CGRmax) and minimum total CGR (CGRmin) was calculated for a range of different compositions, i.e. delta = CGRmax/CGRmin.
For instance, if delta is 2, the maximum total CGR is twice as large as the minimum total CGR for a given wellstream composition. In practice, this means that there can be a difference of up to 200% (!) between the measured and normalized CGR – i.e. CGR normalization is very important. If delta is 1 (or very close to 1), on the other hand, the difference between CGRs (normalized vs measured) is less important (for the range of Psep, Tsep studied).
Fig. 1 presents the sensitivity (delta) to changing separator conditions versus solution CGR. Each point on the figure represents one fluid composition, and as seen, changes in separator conditions can have a significant effect on the reported CGR – specially for leaner gas condensate systems, i.e. <100 STB/MMscf.
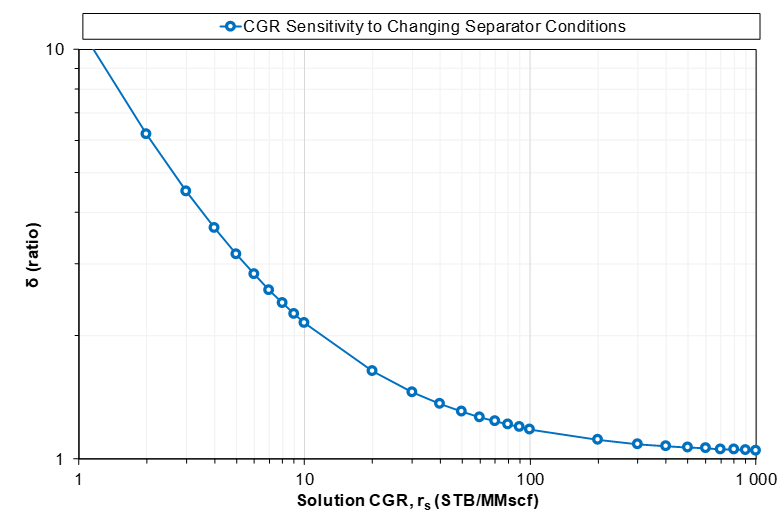
CGR Normalization – Procedure
CGR normalization usually consists of two steps: (1) estimate the flowing wellstream composition based on the measured data and (2) re-process the estimated wellstream composition using a common surface process for all wells. Generally, CGR normalization requires (1) a properly tuned EOS model that matches relevant fluid properties of a specific reservoir or basin, (2) measured CGR, (3) measured separator conditions (pressure and temperature) and (4) a reasonable estimate of the flowing wellstream composition.
The common surface process can be (1) a multi-stage flash process, (2) a K-value based surface process modeling the actual process plant (e.g. where K-values are obtained from a converged process simulation) or (3) a full process modeled in a process simulation application (e.g. HYSYS/UNISIM). The normalized CGR is then computed using the total gas and total oil coming out of this common surface process.
CGR Normalization – Field Example
Fig. 2 shows CGR normalization applied to a well in the Eagle Ford producing from a lean gas condensate fluid system. Separator pressures are decreasing from 1000 psia to 250 psia in ~1000 days, as seen in Fig. 2a. If the changing separator conditions are not accounted for, it looks like the CGR decreases significantly from day 1. However, after applying CGR normalization, much of the relative decrease in CGR is reduced, as seen in Fig. 2b. This is a good example of when CGR normalization has a large impact in general, which is expected as the separator conditions are changing significantly, and the fluid system is relatively lean.
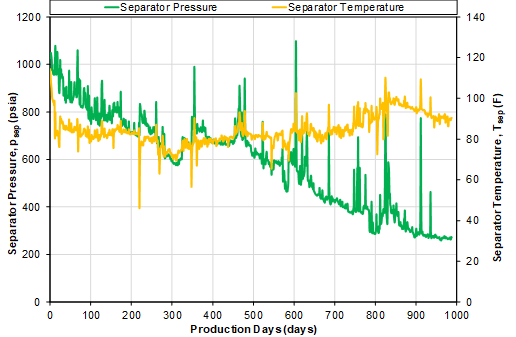
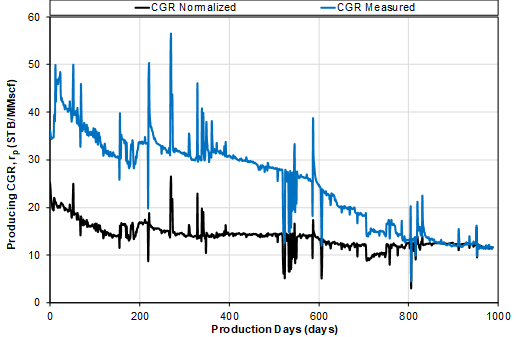
Summary
- CGR normalization is in general not important for black- and volatile oil systems. However, it may be very important for near-critical fluids and gas condensate systems.
- CGR normalization is especially important when i) both “produced fluid properties” (GOR, liquid API) and ii) separator conditions change significantly over time.
- The proposed normalization scheme can be used to calculate a set of consistent oil and gas rates for every well that can be used for CGR performance analysis and history-matching purposes.
- Additionally, as surface volumes are a function of the separator process, it is recommended to define a common surface process for an entire field or basin to ensure consistent apple-to-apple comparison between wells. This common surface process would be used whenever any surface rates are reported for any work (e.g. well tests, PVT experiments, reservoir simulation) related to the field.
[1] Total CGR: cumulative CGR after being processed to stock tank conditions, units: STB/MMscf
Learn more about our consulting capabilities
###
Global
Curtis Hays Whitson
curtishays@whitson.com
Asia-Pacific
Kameshwar Singh
singh@whitson.com
Middle East
Ahmad Alavian
alavian@whitson.com
Americas
Mathias Lia Carlsen
carlsen@whitson.com
About whitson
whitson supports energy companies, oil services companies, investors and government organizations with expertise and expansive analysis within PVT, gas condensate reservoirs and gas-based EOR. Our coverage ranges from R&D based industry studies to detailed due diligence, transaction or court case projects. We help our clients find the best possible answers to complex questions and assist them in the successful decision-making on technical challenges. We do this through a continuous, transparent dialog with our clients – before, during and after our engagement. The company was founded by Dr. Curtis Hays Whitson in 1988 and is a Norwegian corporation located in Trondheim, Norway, with local presence in USA, Middle East, India and Indonesia