SPE-200396: Gas EOR Processes in Tight Unconventionals
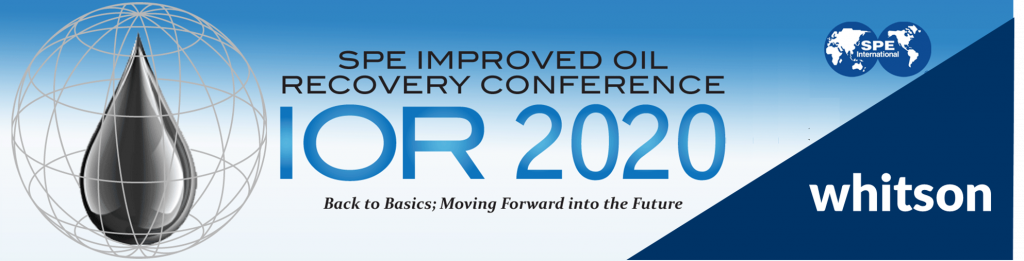
Q1) Why did you select the “minimum dimension” instead of “surface to volume ratio” to explain the dependence of the oil-recovery results on sample size.
Hassan Dehghanpour (University of Alberta)
We believe that the minimum dimension is easier to understand and relate to than the surface-to-volume ratio (S/V). In general, they indicate the same trend, i.e. a smaller minimum dimension is equivalent to a larger S/V ratio, both yielding a larger recovery for the Huff-n-Puff process. Take the example from our paper where we modeled a 1x1x1 ft3 cube, and a 1x5x150 ft3 slab. The general formula for the surface-to-volume ratio of a cube-shaped object can be expressed as
$${V} = xyz, S = 2 (xy + xz + yz), \frac{S}{V} = 2\frac{xy + xz + yz}{xyz}$$
Referring to Fig. 8 (bottom right) in our paper, we can see that the recovery from a 1 ft cube is equal to a ~0.66 ft slab (minimum dimension). For a slab with dimensions of 0.65x5x150 ft3, the S/V = 3.44. If we back-calculate the resulting minimum dimension for a cube having an S/V = 3.44, we get x = 1.74. From our plot, a cube of 1.74 ft results in a recovery of 36.5%, which is less than 38% coming from a 1-ft slab. We believe that both parameters could have been used interchangeably to explain the same trend of ultimate incremental recovery versus rock-size geometrical dimensions. The use of minimum dimension is preferred because it is readily understood physically.
If you know of a situation when minimum dimension would give a misleading quantitative understanding of HnP EOR process where the S/V ratio does not, we are keen on knowing about this situation and would, if it exists, consider emphasizing the difference in S/V ratio and minimum dimension (and perhaps avoid using minimum dimension as a key parameter).
Another less quantitative argument for the minimum dimension is that mass transfer, regardless of the mechanism being diffusion or advection, will always take the path of least resistance. Under the assumption that effects on flow by gravity is negligible (okay in tight matrix), the shortest path from source to sink in a homogenous media is in the direction of the dominant pressure/compositional gradient, i.e. the minimum dimension.
Q2) The paper by Raterman et al. from ConocoPhilips (URTEC) in 2019 took long cores through the fracked region of a well. In that case, they show well that there are numerous fracture clusters with primarily planar fractures… not a shattered region. The area of contact is still large because of the many planar fractures so you can still get some incremental recovery by molecular diffusion, which I agree is likely important in ultra-tight shale reservoirs. What evidence do you have that rock is in fact shattered at depth in actual shale wells?
Russel Johns (Penn State)
This is an excellent point and is something that we agree with. We have discussed the “shattered volume” concept in earlier publication by treating this volume as a region of rubblization/debris. However, we have also consistently argued that the shattered volume must consist of rock pieces where the minimum dimension of the rock pieces are sufficiently small for molecular diffusion to drive the injection-gas components in to the rock and substantially mix with the reservoir fluid in the matrix pores. As we tried to explain in the presentation, we believe the exact geometry is less important, meaning the shattered volume could very well be a series of small slabs, just like the Raterman et al. (2019) paper suggests. The density of fractures for some of the wells reported in that paper were as high as 1 fracture/ft. Slabs with this minimum dimension will, according to our modeling results, yield a substantial incremental recovery by HnP.
Q3) Is it the dimension or the influx surface area that controls the recovery? Example is a complex vs a discrete fracture
Reza Fassihi (BHP)
We argue that it is the dimension, but both parameters are closely related. The smaller dimension you have, the more surface area you have generated.
Q4) Regarding F2F vs HnP—was your time horizon on your graph when the F2F recovery overtakes HnP is ~1500 days?
Robin Watts (Messer Americas)
For the particular comparison case in the paper, F2F overtakes HnP at approximately 1750 days.The time efficiency of F2F is dependent on matrix rock permeability and distance from injector-to-producer hydraulic fracture. The higher the perm and the short the F2F distance, the faster F2F RF will equal HnP RF and thereafter continue to grow much faster than HnP.
Q5) How can we do Fracture to Fracture flow in practice? How to inject gas in alternate fractures?
Mohan Kelkar (The University of Tulsa)
It will require some form of completion in the lateral with a valve configuration such that injected gas and produced fluids can be directed through every other fracture. To our knowledge, there is one company in Calgary who are currently developing such tools. There are also several patents on F2F completions.
Q6) In the F2F process, do you need to assume there are no high-perm features (e.g. fractures) connecting 2 hydraulic fractures? If so, do you think that is a good assumption?
Todd Hoffman (Montana Tech)
In the current model, we have assumed no “short-circuiting” of the hydraulic fractures. Fractures or high-permeable conduits of any kind between two planar hydraulic fractures are of course a possibility, and this may cause a reduction in the efficiency of F2F. However, we study F2F as a cyclic process (just like HnP) with periods of dedicated injection and periods of dedicated production. The cyclic process will definitely help reduce “short circuiting” of the injected gas. The short circuit volumes are very small even though they may have significant conductivity. They will quickly fill up completely during the injection cycle, and thereafter injected gas will move into the rock, displacing oil towards the producing fractures (pressure sinks). The miscible efficiency is not lost because of short-circuiting, but the conformance can be severely affected (not necessarily in a negative way). We have several studies dating back to 2013 that try to quantify the impact of F2F short circuiting.
Q7) Instead of single horizontal-well F2F process, why not just conduct cross (horizontal) wells displacement-type injection?
Chao-Yu Sie
For the assumption of large planar hydraulic fractures that are tip-to-tip generated from two horizontal laterals in parallel, the conformance (i.e. areal and vertical sweep) of a gas-based, displacement-type process will be potentially be very low for a well-to-well configuration (i.e. parallel to the hydraulic fractures), and highest for a fracture-to-fracture configuration (i.e. perpendicular to the hydraulic fractures). If the hydraulic fractures are generated in a “perfect” zipper pattern, then one could in theory inject from one well, and produce from the other.
Q8) Fracture-to-fracture success would depend on a uniform distribution of the SRV around each hydraulic fracture. In reality, you have a dominating fracture that would steal most of the injected gas. Any comments?
Reza Fassihi (BHP)
Perhaps, we don’t quite see your point. The F2F process is primarily achieving oil recovery in the non-shattered volume between the shattered volumes (if existing) of the injector fractures and producer fractures.
Q9) In your experience, is your approach useful as a predictive GCEOR tool, or simply as a model to fit data once you have acquired the field data?
Brent Thomas (Stratum Reservoir)
By “GCEOR”, we guess you mean “tight unconventional gas EOR”. Any model is predictive only to the extent that it reflects accurately the larger- and smaller-scale geology, spatial distribution of petrophysical properties, and proper treatment of the physics and thermodynamics of gas-oil phase behavior (diffusion and gas-oil phase equilibria). Our modeling tools as outlined in this paper would become more predictive as the information mentioned above becomes more accurate and relevant. For PVT, as an example, having an EOS model that is tuned to relevant PVT data for a gas EOR process would be more reliable in defining key recovery PVT properties (e.g. saturation pressure vs added injected gas amount, solution oil-gas ratio of gas phase, and perhaps oil swelling) than if depletion-only PVT data were used to tune the EOS (e.g. DLE, CCE).
Q10) Does the grid type affect the produced composition profiles?
Saeid Khorsandi (Chevron)
The grid type selection is important to capture the physics of gas EOR processes, and accordingly, “yes” we believe they are very important to correctly modeling gas EOR. Clearly the properties assigned to grid cells in each grid type is equally important, as well as capturing the physics correctly (difficult for diffusion coupled with complex phase equilibria).
Q11) Need more well-to-well thinking in this type of work.
Edward Behm (Behm Energy Resources LLC)
Previous reports of field tests with well-to-well (W2W) displacement between hydraulic fractured wells have not shown promising results. W2W is indeed the best option in conventional miscible gas displacement processes, but for W2W gas EOR to succeed in tight unconventionals, it will be necessary to quantify the connectivity and resulting areal sweep efficiency (conformance). We believe that W2W versus F2F gas EOR will be most successful where the areal sweep efficiency is highest. We also believe that a cyclic F2F or W2W process will minimize adverse short circuiting (fractures, behind-casing) low-volume/high-conductivity conduits connecting injection and producing locations.